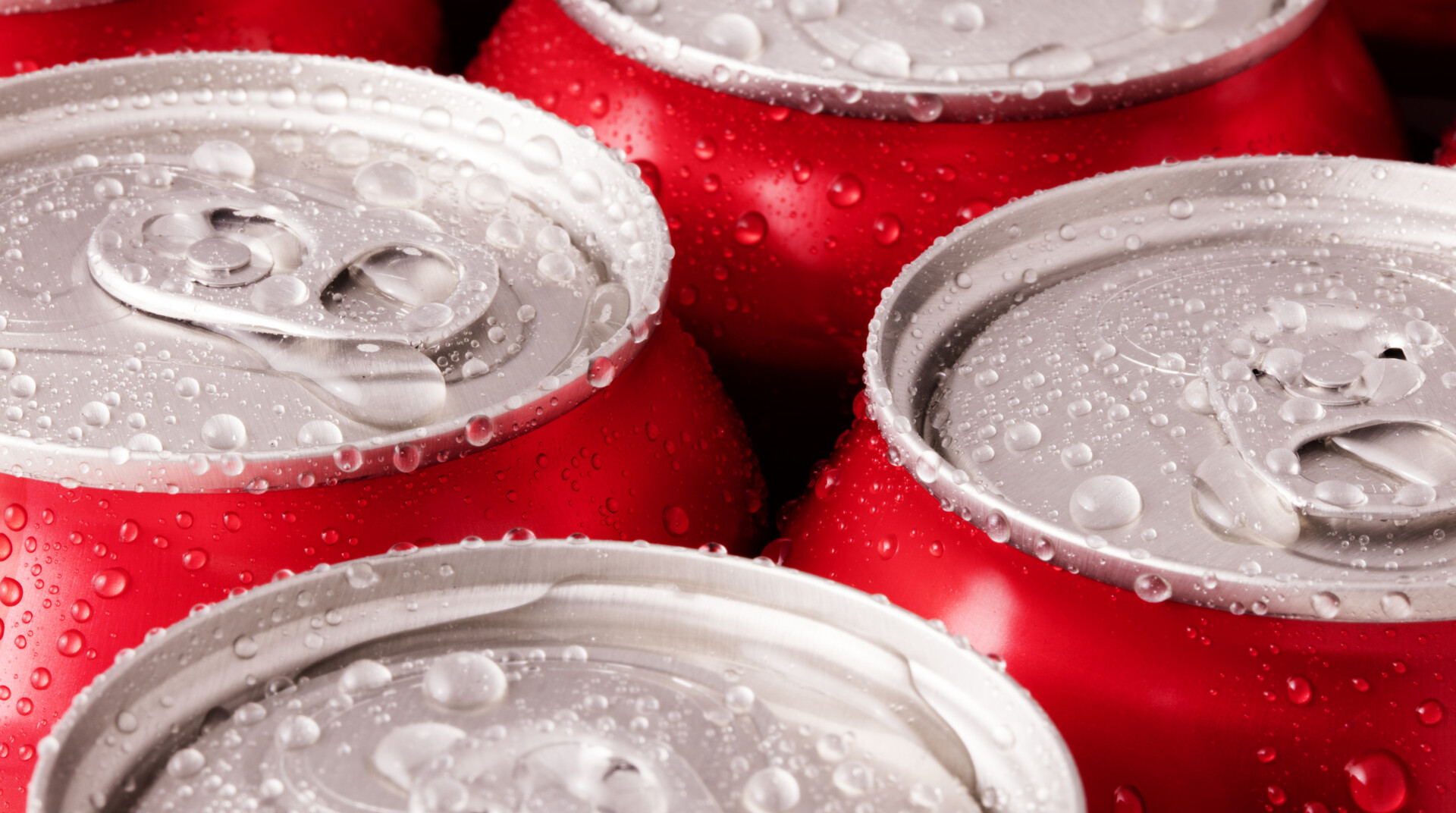
Carbon Footprint of U.S. Aluminum Can Production Down 40%+ Since 1990s
A new comprehensive Life Cycle Assessment (LCA) by sustainability consultancy Sphera shows that the carbon footprint of aluminum cans made in North America has dropped by nearly half over the past three decades.
Decades of Improved Performance
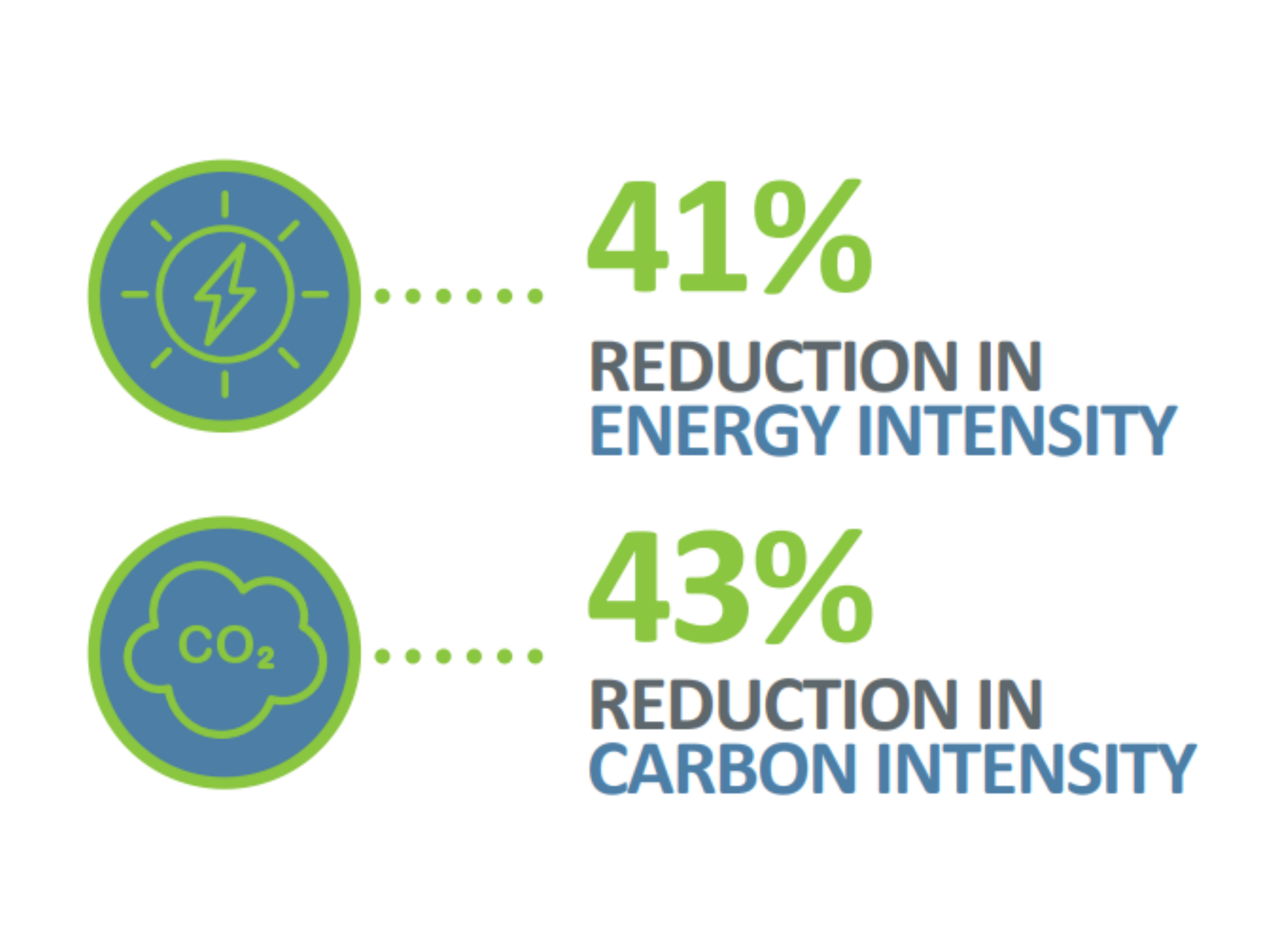
A recent comprehensive Life Cycle Assessment (LCA) by sustainability consultancy Sphera shows that the carbon footprint of aluminum cans made in North America has dropped by nearly half over the past three decades. The Life Cycle Assessment of North American Aluminum Cans found that greenhouse gas emissions for aluminum beverage can production has dropped more than 40% since 1991 and 7% since 2012.
Energy demand has declined by similar levels during this time period. These reductions have been driven largely by decreased carbon intensity of primary aluminum production in North America, lighter cans (which are 27% lighter per fluid ounce compared to 1991) and more efficient manufacturing operations.
Increased Recycling Key to Lower Carbon Impact
Improving recycling rates and increasing the use of recycled material in production could improve the environmental performance of aluminum cans even further. Each percentage increase in the end-of-life recycling rate reduces the carbon intensity of aluminum can production (cradle-to-grave) by 1.02 kg CO2 equivalent per 1,000 cans. And each percentage increase in recycled content reduces the carbon intensity of aluminum can production (cradle-to-gate) by 1.43 kg CO2 equivalent per 1,000 cans.
Recycling a single can saves 1.56 megajoules (MJ) of energy or 98.7 grams of CO2 equivalent. This means that recycling just a 12-pack of aluminum cans will save enough energy to power a typical passenger car for more than three miles. The energy saved by recycling 100% of aluminum cans in the U.S. could power up to 4.1 million homes for a full year. This underscores the critical need for increased aluminum can recycling, which has declined in the United States in recent years.
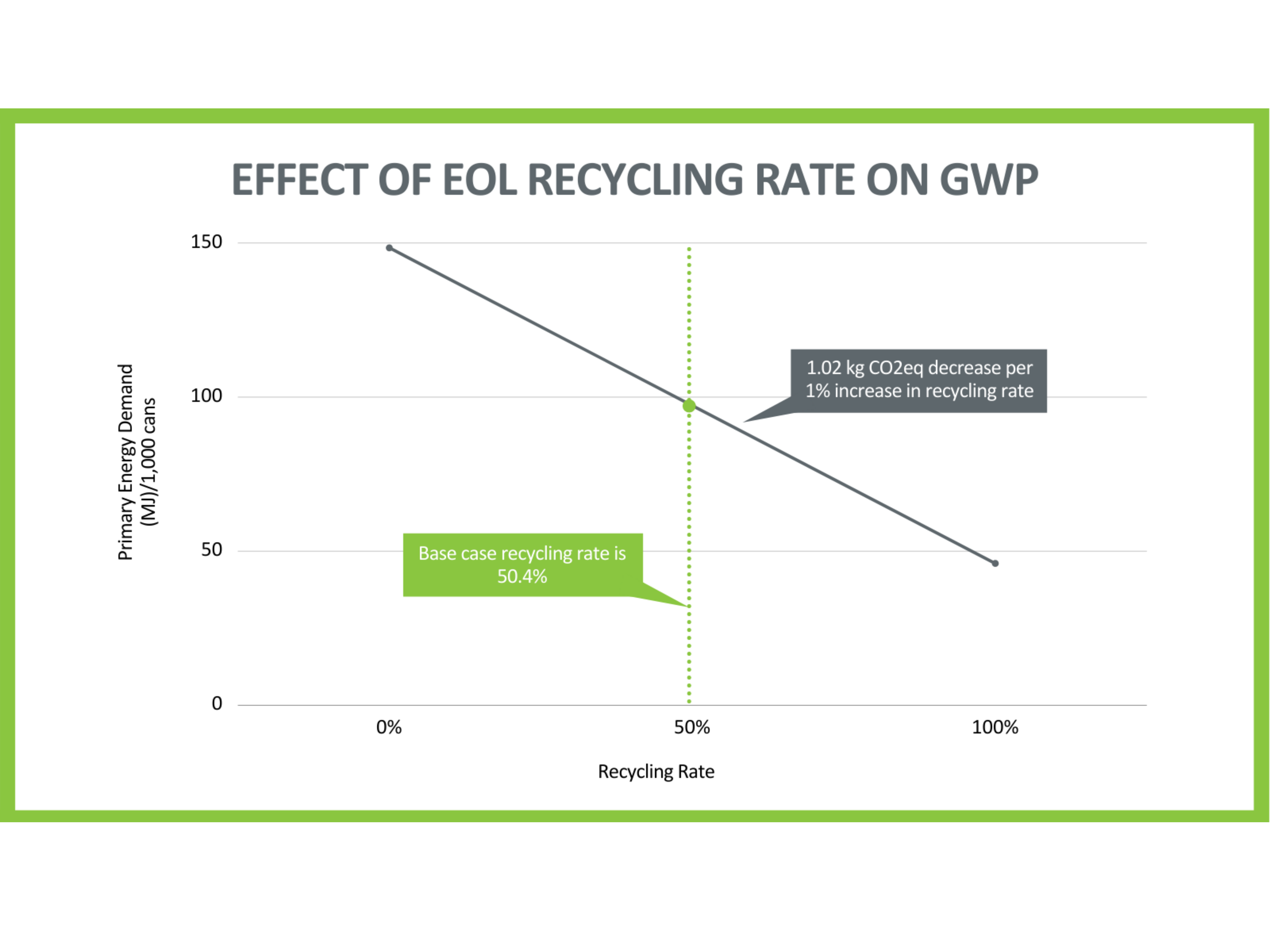
Metal Sourcing Matters
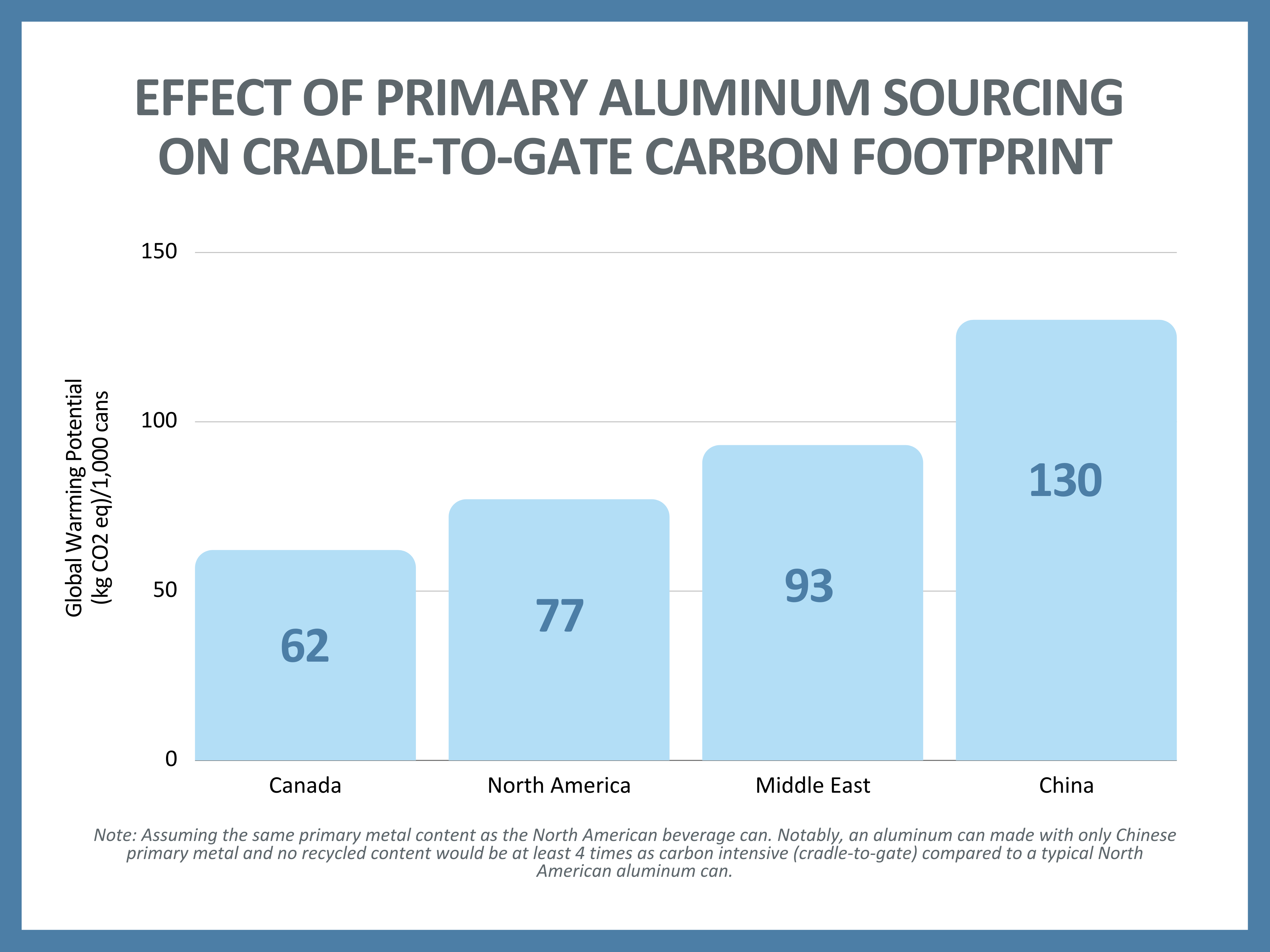
“We determined that sourcing of primary metal is a significant contributor to the product’s overall environmental footprint, even with the current high recycled content of aluminum cans," said Chris Kofler, technical director, Americas at Sphera.
Raw material sourcing has a “significant impact” on the sustainability of aluminum can production, according to the study. For example, while primary aluminum sourced from Canada is made almost exclusively using renewable hydropower; Chinese primary aluminum is made largely with coal-generated power, making it far more carbon intensive.
"Not all primary aluminum is created equal,” according to the report. Notably, a typical aluminum can made with imported Chinese metal is nearly twice as carbon intensive (cradle-to-gate) as a domestically sourced can. And a can made using only Chinese primary metal and no recycled content would be at least 4 times as carbon intensive compared to a typical North American aluminum can.
Learn More About Aluminum Can Sustainability
Aluminum beverage cans are the most sustainable beverage package on virtually every measure. Cans have a higher recycling rate and more recycled content than glass or plastic. They are lightweight, stackable and strong, allowing brands to package and transport more beverages using less material. And aluminum cans are far more valuable than glass or plastic, helping make municipal recycling programs financially viable and effectively subsidizing the recycling of less valuable materials in the bin.
Most of all, aluminum cans are recycled over and over again in a true "closed loop" recycling process. Glass and plastic are regularly "down-cycled" into products like carpet fiber or landfill liner — a process that can generally happen only once.
The Aluminum Association releases an annual Key Performance Indicator (KPI) report tracking a number of metrics on the can's sustainability performance compared to competing packaging types.
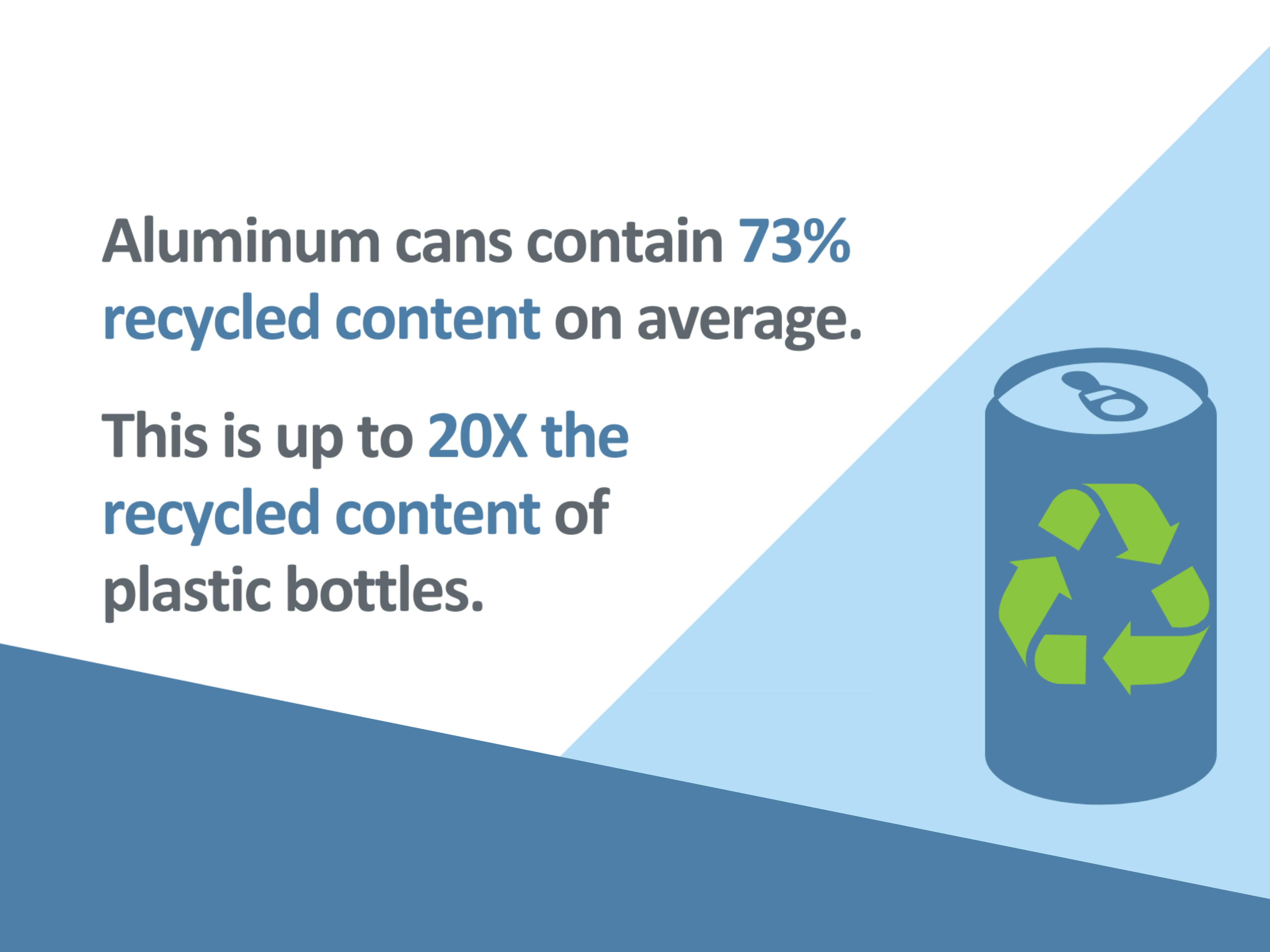